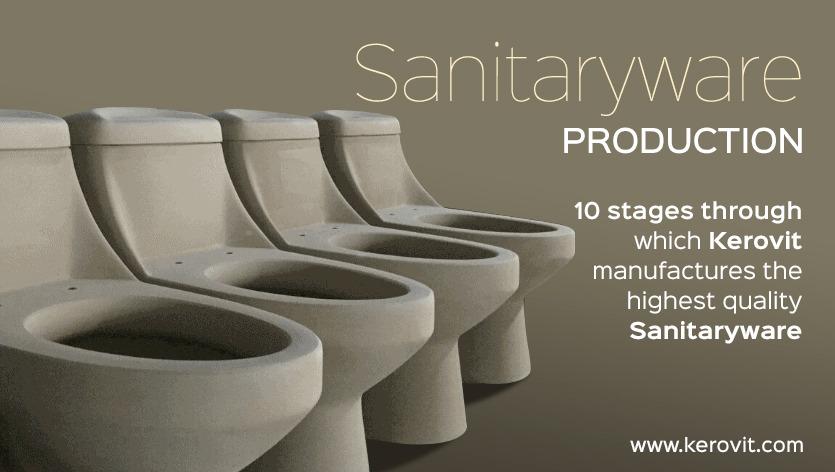
Sanitaryware Production – 10 stages through which Kerovit manufactures the highest quality Sanitaryware
Starting from the body preparation up to the packaging stage, here’s all about the production process of creating world-class sanitaryware at the Kerovit manufacturing plant.
Preparing a robust body – Body Preparation
Body preparation is the first step in the sanitaryware production process, where slip is created by mixing ball clay, silica, China clay and feldspar. This composition is called tri-axial body and consists of a flux, body former and filler. The external cladding is made of plastic material, and the non-plastic filler provides strength after the ceramic firing. The Flux material maintains the glass at a lower temperature, meaning that we don’t need to heat up the interior of the oven quite so much. This saves energy and ensures optimum use of gas and electricity.
After the slip preparations are complete, we check for parameters like thixotropy and fluidity. These parameters are subject to change based on factors such as casting, required casting rate, composition and climate.
The culmination of scrap slip, virgin slip and runoff slip create a supply slip. Based on the required casting rate and availability of the scrap slip, the composition is liable to change.
Prior to the body being sent to the slip storage silos, we ensure that the slip preparation is efficiently done, meeting all the parameters. The casting department of our manufacturing plant then takes over and continues with the casting process.
Glazing it up – Glaze Preparation
The processes of body preparation and glaze preparation take place simultaneously. During this stage, we prepare the glaze for our plant’s spraying section. Depending on the requirements, the glaze is prepared in different colours, using raw materials such as china clay, quartz, calcite, zinc oxide, feldspar and zircon. These raw materials are grounded in a ball mill and before it is unloaded from the ball mill, we test the particle size as well. Aluminium Oxide, also known as Alumina, is used in ball mills due to its strength. The coarse particles and iron particles are removed by passing the glaze through sieves and magnets respectively. To check the glaze’s final colour, we carry out sample spraying and the fire process.
We ensure that before being used in production, the glaze meets necessary standards and is approved by an authorised laboratory. To achieve the required properties while spraying, the glaze is mixed with a binder. For getting the perfect spray quality, we properly maintain the density, viscosity, fluidity and drying time.
Moulding to perfection – Mould Preparation
The glaze preparation stage is followed by the moulding preparation, wherein we create the perfect size and shape of the body before it’s sent out for the process of casting. Cast plastic moulds are used in case moulds, which are sent from the case moulding section to the moulding section of the plant. By mixing plaster of paris and water in a 4:3 ratio, the preparation of the mould begins. However, this ratio is not absolute and might be subject to change depending on factors such as required mould strength and the plaster’s purity. Having prepared the mould, there is often a possibility of excess water presence, which is efficiently removed in the drier – this is an imperative stage for increasing the longevity of the mould. Owing to high absorbent properties, Beta plaster is used in the making of the mould. Also, we use Resin mould for high pressure casting.
The right casting for sanitaryware – Casting
When it comes to sanitaryware, there are various types of casting; low pressure and high pressure casting, normal bench casting, beam casting and battery casting. All these types have their individual pros and cons. However, it would interest you to know that all these types of casting follow the same exact process wherein the mould is filled with the slip and a casting layer is created on the mould. Using the drain hole, any excess slip is properly drained. Following this, the casted ware is dried and released from the mould – during this stage, the ware is called Greenware, which is dried in atmospheric temperature for up to 3 days, before being sent out to the drier. Before the drying phase begins, we ensure to carry out final checks in terms of smooth joint edges, improper finishing, small cracks and pinholes. Prior to the drier stage of sanitaryware production, the greenware’s moisture quantity varies from 12% to 22%.
Time to dry up – Drying
During this phase of the production process, the greenware is properly enhanced by getting rid of the mechanically induced water content from the ware. After this, the moisture quantity of the ware goes down to somewhere between 1.5% to 0.5%. The duration of the drying process typically ranges from 6 to 12 hours. There are usually two kinds of driers that are used – batch drier and tunnel drier. In case of the tunnel drier, the ware is constantly fed to the drier and is simultaneously discharged at the other end. On the other hand, the batch drier is loaded and unloaded all at once. The ware shrinks in size and loses all excess weight through an atmospheric heating process, wherein the temperature is between 110 degree celsius to 120 degree celsius.
Spraying with Control – Control & Spraying
During this stage, the ware is properly inspected for any evident defects quality wise. If any defects are found, the ware is either repaired or discarded depending on the magnitude of the defect. We make use of Kerosene to detect defects in the wares and upon clearing the inspection stage, the most well made wares go for the spraying process.
Spraying is made possible with glaze and for our premium sanitaryware range Aurum Collections , we use different coloured sprays on the wares. We use both manual and state-of-the-art machinery in order to execute the spraying process. Upon completion of the spraying, the ware is dried for some minutes before it goes for the logo printing.
Fire it up – Firing
The sprayed ware is then loaded into the Kiln machine. Using an air blower or vacuum, any dust and impurities are removed from the wares. The maximum temperature of the Kiln is usually 1250 degree celsius. At Kerovit’s sanitaryware manufacturing plant, we use a Tunnel Kiln for the firing stage of the production process. Sanitaryware Kiln has three primary zones – preheating, firing and cooling zones. All the mechanically and chemically combined water is removed from the ware in the preheating zone. In the firing zone, the glaze is fused evenly and all the raw materials are fused together. Finally, in the cooling zone, a glossy surface is created through sudden cooling. After the wares go through the firing process, they go to the sorting area.
Getting it all sorted – Sorting
As the name suggests, every single ware from the tunnel kiln is checked and sorted according to the defects. In case of minor defects such as pin holes, cold fill is used to repair it. Following this, all the wares that are free of defects are sent for packaging. At Kerovit, quality is our top priority and hence this final quality check is imperative in order to maintain an uncompromised standard. We also conduct random sampling for a leak test, flush test, load test and smoke test.
Reworking the nitty gritties – Reworking & Refiring
Any wares that require minor repairs are sent to the rework department of our factory and depending on the requirements, some are sent to the tunnel kiln. Upon completion of the reworking and refiring process, the wares go through yet another round of inspection. Once the quality standards are met, the wares are finally sent to the packaging section.
Pack up! – Packaging
And lastly, we arrive at the final stage of the sanitaryware production process – packaging. Here, the wares that have passed all the quality checks and meet international standards, are packaged and transferred to our warehouse.
We hope you enjoyed this journey of Kerovit’s step by step sanitaryware manufacturing process! If you like to know more about the production process and parts of faucets then visit our website.